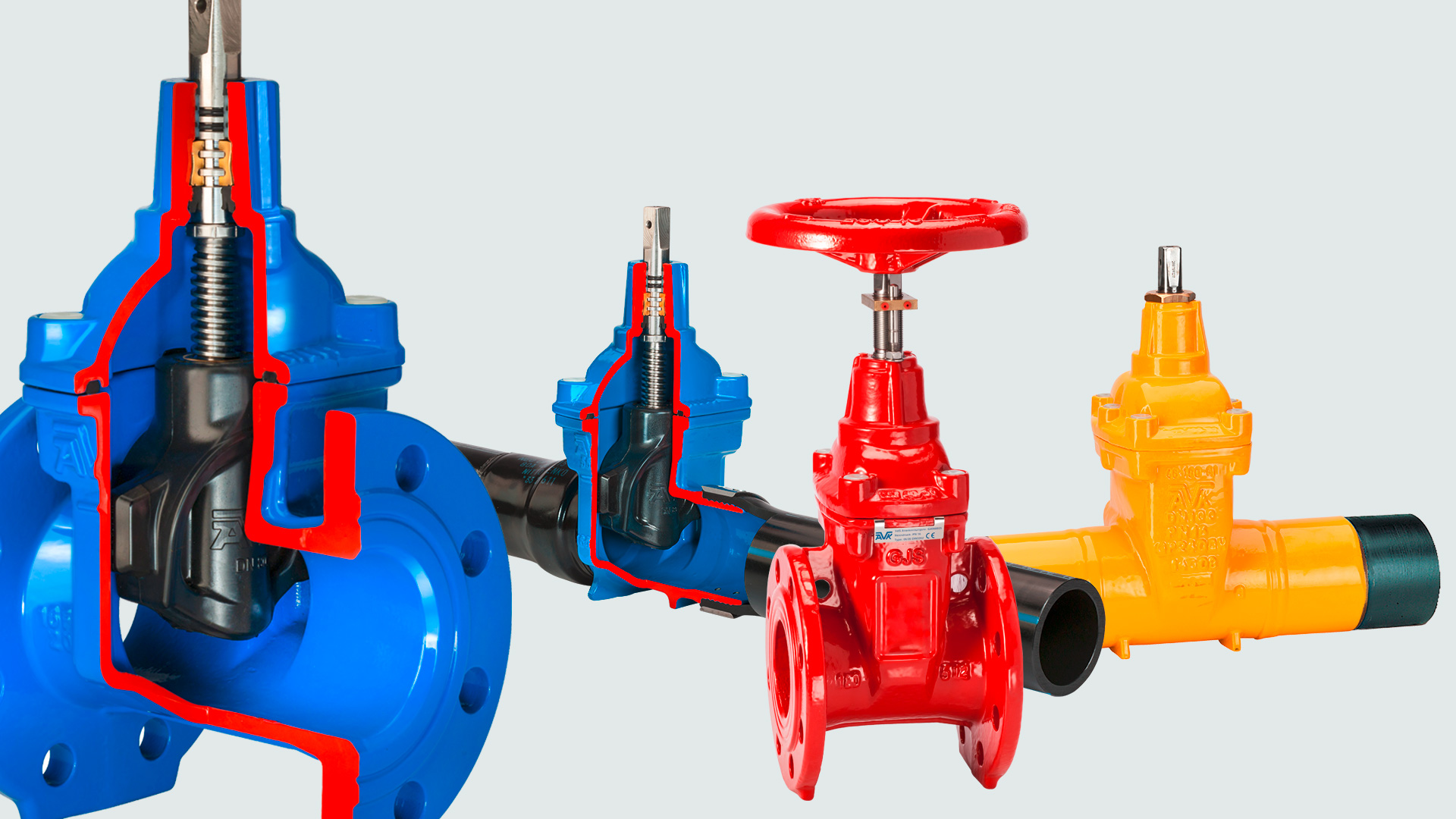
Intro to AVK Gate Valves
Gate valves renowned for superior quality
AVK has been in the valve business for 50 years. When Niels Aage Kjaer took over his father’s smithy in 1970, he developed the first gate valve, a resilient seated socket ended gate valve with a lot of new technical features. He soon realized that the quality of the internal rubber components is of paramount importance for the valve performance, so back in 1975 he decided to take full control of this and acquired a neighbouring rubber factory. Today, AVK GUMMI A/S develops and manufactures rubber compounds to AVK.
High quality gate valves
AVK's continuous focus on high quality and innovation has paved the way for a global reach, and the gate valve range has been widened substantially to meet local requirements around the world. Today, AVK offers gate valves according to global standards and with a wealth of end connections and material configurations – in total more than 300 variants in total from the AVK Group of companies.
Design features of AVK gate valves
• Fixed, integral wedge nut prevents vibration and ensures durability.
• The ductile iron core is fully vulcanized with drinking water approved EPDM rubber, no iron parts are exposed to the medium and the excellent rubber vulcanization prevents creeping corrosion underneath the rubber.
• Guides in the wedge and on the valve body ensure a uniform closure, safe operation and prevent overloading of the stem.
• The wedge has a large through bore with room for the stem, completely free of hollows or cavities where stagnant water or impurities could collect and cause contamination.
• Stainless steel stem with wedge stop and rolled threads for high strength.
• Full circle brass thrust collar provides fixation of the stem and low free running torque.
• Triple stem seal system with an NBR wiper ring protecting against impurities from outside, a polyamide radial bearing with four NBR O-rings and innermost an EPDM rubber lip seal as the main hydraulic seal to the flow.
• Round bonnet gasket fixed in a recess groove in the bonnet preventing it from being blown out by pressure surges.
• Counterbored and hot-melt sealed bonnet bolts encircled by the bonnet gasket ensures no risk of corrosion.
• Full bore.
• Epoxy coating to DIN 30677-2, GSK approved.