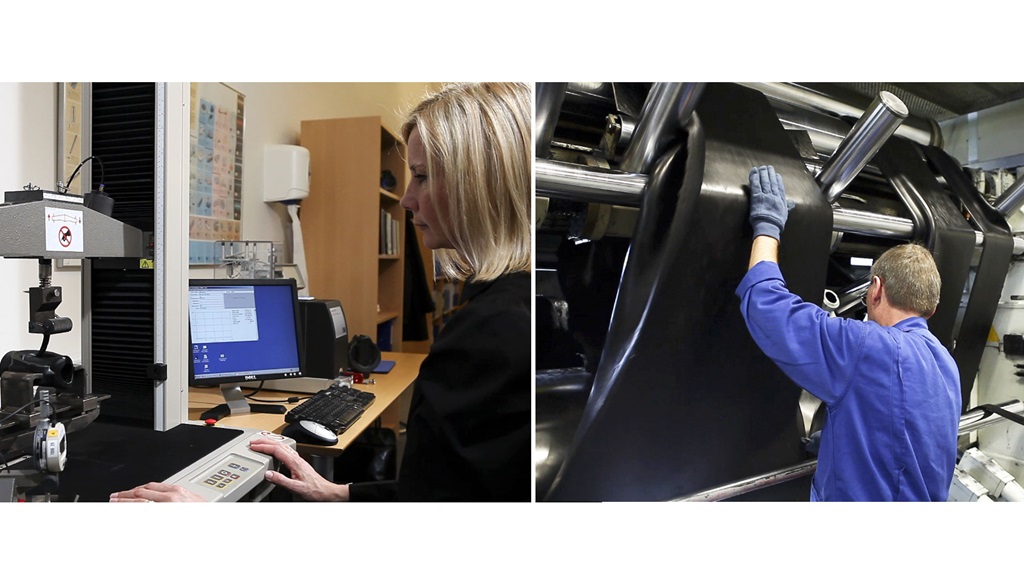
AVK’S Unique Rubber
AVK rubber - a seal of quality
For over 40 years, AVK GUMMI has developed rubber components for the water, natural gas, healthcare and food industries. By maintaining complete production control through our high-tech facilities and one of the world's most advanced mixing plants, we can offer unique rubber compounds of exceptional quality and uniformity.
AVK’s own rubber with uncompromising standards of excellence
No matter which industry you are in, it is essential that the rubber components inside your valves, hydrants and couplings are of the highest quality to ensure a safe, watertight seal and trouble-free operation, even after many years without use. Through our rubber factory, AVK GUMMI A/S, we develop and produce our own rubber components to make absolutely sure they meet and exceed our customers’ standards. Our valve design and other market-leading innovations provide the reliability you need to safeguard your network and the health and safety of your customers. This is especially important for drinking water network operators, who can only be sure of an uncontaminated supply by choosing a valve supplier that gives such priority to quality and compliance.
Compression set with unique ability to regain original shape
AVK’s rubber compounds have an excellent compression set, which means the ability to recover the original shape after having been compressed. Even after many years of operation, tiny pebbles, sand and other impurities will not affect the rubber surface or the tightness of the rubber.
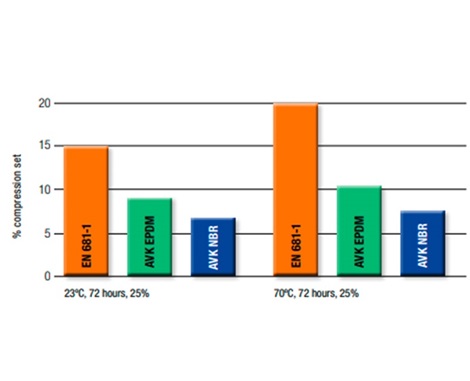
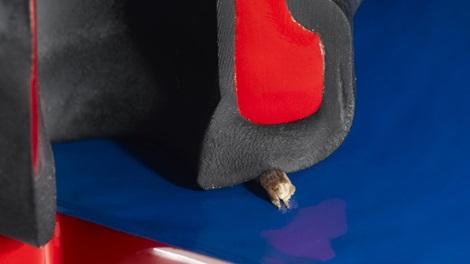
Test method for permanent deformation
Test method for permanent deformation
The rubber is deformed by 25 % of its original thickness at a constant temperature for a specific time. The pressure on the rubber is relieved and the layer thickness is measured after half an hour. The smaller the deformation, the better the memory effect.
Compression set (S) =(d0 - d1)/(d0 - d1)
• d0 = original thickness of the test specimen
• d1 = thickness of test specimen after test
• d2 = thickness of test specimen in compressed condition
RESISTANCE TO WATER TREATMENT CHEMICALS
Chlorine and other chemicals are commonly used to clean new pipelines or disinfect old ones. Ozone and chlorine may also be added in low concentrations to make the water drinkable. AVK has developed an EPDM rubber resistant to such water treatment chemicals.
Thoroughly tested rubber compounds
The rubber which is a complex formulation of many ingredients is developed and tested by AVK’s own R&D scientists. For third party verification and approvals, we work only with recognized test institutes. AVK has the most advanced state of the art mixing facility which ensures repeatability and high performance materials.
Tests are continuously carried out to ensure that the correct rubber compound is applied for the right area of use, and that rubber used in drinking water does not give off taste, smell or colour. The rubber compounds are also ozone tested as exposure to ozone tends to have a negative effect on NBR as an example.
Ozone resistance:
Ozonation is commonly used to reduce smell and taste or to reduce bacterial activity. The chemical reaction will also cause degradation
of rubber materials, if such materials are not adequately formulated to encounter highly reactive chemicals such as ozone.
AVK’s own compound EPDM is superior to any other material, including many other EPDM materials. The unique structure can withstand an extremely high concentration of ozone.
After 200 hours of exposure in 200 pphm the properties of AVK’s EPDM have not changed, while both the SBR and NBR grade are suffering.
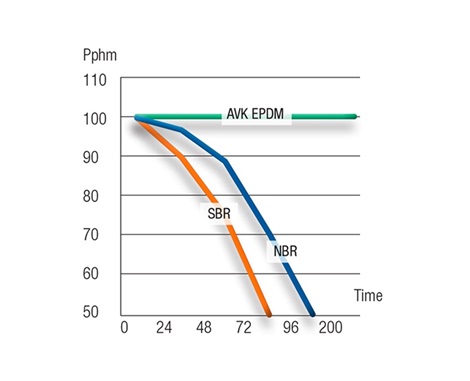
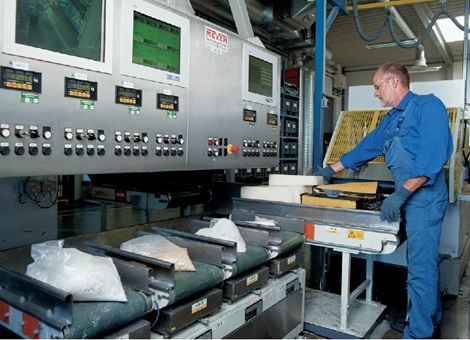
As chlorination of drinking water is common in most places it is important that the rubber is not affected by long time exposure. AVK has developed a series of EPDM compounds - here illustrated by AVK EPDM which is literally unaffected by even extreme concentration of sodiumhypochlorite (NaOCl) - a commonly used source for chlorination.
In the past, SBR was often used for wedges, as this material is tough and cost efficient. However, SBR is inferior to AVK’s EPDM not least due to the poor resistance towards chlorination. NBR is often requested since this rubber type may be used for both water and gas applications, provided that the compound has been approved accordingly. However, a compromise must be accepted as NBR - in this case AVK NBR - will also suffer.
Avoid contamination Minimize formation of biofilm
Formation of biofilm: Organic substances such as medicinal paraffinic oils and waxes migrate from the rubber compound. They act as nutrients for microorganisms, which will then start forming biofilm. In the course of time, however, there will be fewer nutrients available, and the biofilm will decompose.AVK’s EPDM rubber recipes are composed with focus on minimising the formation of biofilm. The rubber will therefore not provide breeding ground for bacteria.
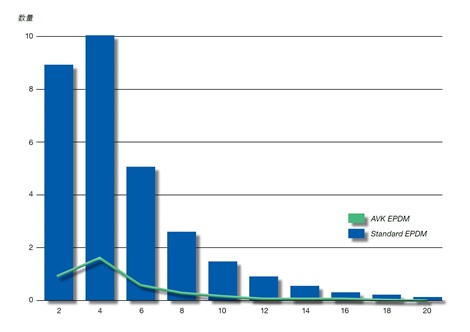
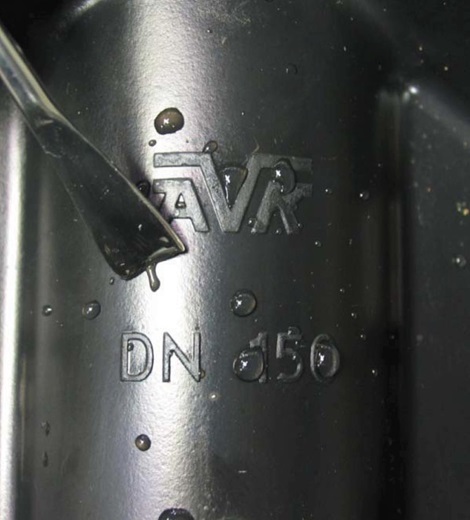